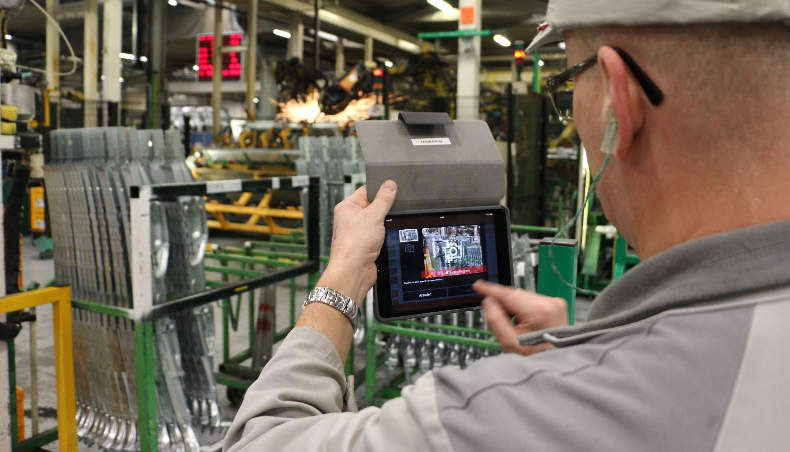
TÉMOIGNAGE
« C’est devenu une marotte, on parle d’internet industriel des objets un peu partout… Mais quand beaucoup discutent, les équipes chez Renault, elles travaillent. Le projet « Connected Plant » prend à la racine, la question de la standardisation des protocoles, de la description et de la présentation des données pour créer un réseau de ressources digitales exploitables par toute une profession.
Le chantier « Connected Plant »
La situation a progressivement conduit à multiplier les réservoirs de données qui, alimentés par différentes sources au gré des besoins (ce qui aboutit à des pertes de temps), impose la duplication des workflows et accroît les risques de dé corrélation des informations.
Tant du côté des techniciens qui mettent en place les sources de données que du point de vue de ceux qui réutilisent les informations, un modèle vertueux consiste à décloisonner les silos et à structurer un réservoir de données unique où chacun aurait la possibilité de puiser les données qui l’intéresse. Il s’agit en effet, d’arriver à constituer une ressource numérique globale dans laquelle les données sont collectées une seule fois et ensuite, réutilisées autant de fois et aussi souvent que nécessaire pour répondre à des besoins d’information extrêmement diversifiés dans le domaine de la maintenance, de la qualité, de l’automatisation, de la planification, de la consommation énergétique, etc. La démarche vise à piloter les processus par la donnée.
Début 2017, pour mettre en place le chantier « Connected Plant », le groupe Renault a constitué un groupe de travail composé d’un expert de l’OT et de deux experts de l’IT, l’un spécialisé dans le matériel et les infrastructures et l’autre dans ce qui relève des ressources logicielles et des systèmes. La réunion de ces profils reflète le resserrement des liens qui unissent les métiers de l’informatique et ceux des technologies numériques opérationnelles.
Suite à une analyse approfondie des technologies au cours de benchmarks entre grands industriels parmi lesquels figurent notamment, Edf et la SNCF, dès juillet 2017, le groupe de travail a identifié OPC UA comme un standard de référence pour unifier la connexion des sources d’informations avec le réservoir de données du groupe.
Une passerelle dédiée pour les usines
Pour créer un canal de communication universel permettant de récupérer les jeux de données opérationnelles, les équipes de Renault ont réalisé un co développement avec PROSYST pour les automates Schneider Electric et Siemens. Ils ont commencé à travailler sur des îlots comportant plus d’une dizaine de robots industriels Fanuc et un automate programmable à pupitre Siemens, n’offrant aucune compatibilité avec OPC UA.
La pile de protocoles et les ressources logicielles contenues dans OPC UA permettent d’encapsuler les modèles de données pour acheminer des jeux d’informations complets vers un réservoir de stockage communément appelé Datalake par les équipes du constructeur automobile.
Le co développement avec PROSYST a débouché sur la mise au point d’une passerelle pour objets connectés : l’IoT Box, qui est un système client-serveur OPC UA communiquant directement avec les différents réservoirs de données du groupe.
La technologie OPC UA a été implantée en Espagne dans l’usine de Valladolid pour connecter cinq îlots robotisés, ainsi qu’en Turquie dans celle de Bursa comme en Roumanie dans l’usine Dacia de Pitesti, afin de connecter à chaque fois une vingtaine d’îlots. Ces sites totalisent 505 robots industriels générant quarante-cinq variables.
Elargir les modèles de donnés à d’autres équipements
Au cours de l’année 2018, d’autres équipements ont été visés par le projet « Connected Plant ». C’est le cas notamment des quelques 6000 visseuses qui sont utilisées pour l’assemblage des pièces dans les usines au cours d’opérations qui peuvent être soit automatisées, soit manuelles. Certains de ces équipements sont des visseuses électriques asservies qui, au moyen de protocoles généralement spécifiques à chaque fabricant, produisent ces données (code de process, ordre envoyés, résultat opérationnel, énergie consommée, etc). Si ces outils ne supportent pas nativement les communications au standard client-serveur OPC UA, les fournisseurs qui équipent les usines Renault en visseuses électriques se sont engagés à développer de tels produits en 2019.
Là encore, un modèle de données a été mis au point pour assurer la traçabilité des opérations réalisées au moyen des visseuses pendant l’assemblage des moteurs. La description comprend, entre autres : le numéro du moteur, le type de visseuse, l’unité de couple, la valeur de cette unité appliquée au serrage, etc.
Une autre initiative s’est attelée à la modélisation de la charge des batteries destinées aux véhicules électriques. A la fin de l’année 2018, quelque 80 000 points de mesure ont été connectés au système de collecte en s‘adaptant à la diversité des équipements existants par la mise au point de connecteurs OPC UA spécifiques.
En l’état actuel, l’internet industriel des objets du groupe Renault consiste à connecter les sources de données vers différents réservoirs en traversant d’abord la passerelle IoT box où s’opère la transformation entre les protocoles souvent spécifiques des équipements et le standard OPC UA.
En 2019, le projet « Connected Plant » va s’attacher à modéliser les données dans les lignes de fabrication en créant des descriptifs adaptés aux centres d’usinages, aux tours, aux fraiseuses, et aux machines spéciales, ce qui devrait porter à 200 000 le nombre de points de mesure connectés avec les réservoirs de données du groupe. Le constructeur automobile travaille avec ses fournisseurs pour que ces derniers implémentent OPC UA dans leurs équipements ou qu’ils œuvrent à son portage dans les logiciels embarqués. Dans le même temps, les modèles de données vont être largement partagés afin que tous les sites profitent de la synergie qu’ils apportent pour disposer d’indicateurs fiables, reproductibles et duplicables presque immédiatement.
Pour l’ensemble des équipes concernées par le projet « Connected Plant », les objectifs pour la fin de l’année 2020, consistent à déployer des canaux de communication bidirectionnels qui, de l’objet connectés industriel et des applications IT ou IO, aux centres de stockage, permettent la circulation des données industrielles en s’appuyant sur un protocole unique : OPC UA.
A ce stade, le groupe Renault souhaite créer un standard international de réseau industriel pour les constructeurs et les équipementiers automobiles afin qu’ils soient en mesure d’enrichir et de partager leurs modèles de données partout dans le monde. C’est exactement la fonction que remplit internet dans la sphère publique. »
Découvrez d'autres témoignages :
Des questions ?
Nos experts sont à votre écoute.
OU APPELEZ-NOUS AU +33(0) 3 27 30 59 59
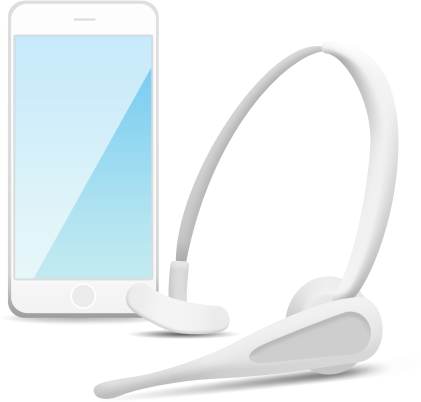